This article will explore the hidden costs of neglecting routine maintenance and emphasize how proactive parts replacement is the ultimate strategy for maximizing uptime and minimizing long-term expenses.
Why Proactive Air Compressor Parts Replacement is Key to Avoiding Costly Downtime
- Home
- Blog
- Why Proactive Air Compressor Parts Replacement is Key to Avoiding Costly Downtime
Start with a relatable scenario: The unexpected compressor breakdown. Hook: Highlight that while immediate repair costs are visible, the true financial drain often comes from unplanned downtime. This article will explore the hidden costs of neglecting routine maintenance and emphasize how proactive parts replacement is the ultimate strategy for maximizing uptime and minimizing long-term expenses.
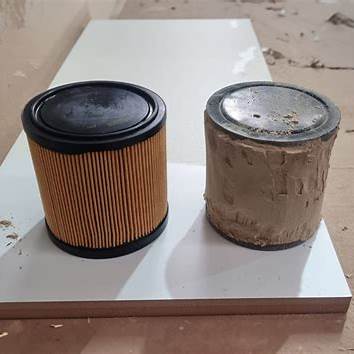
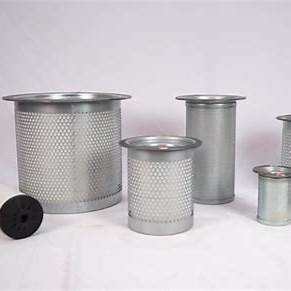
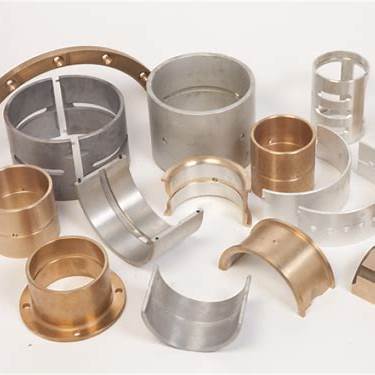
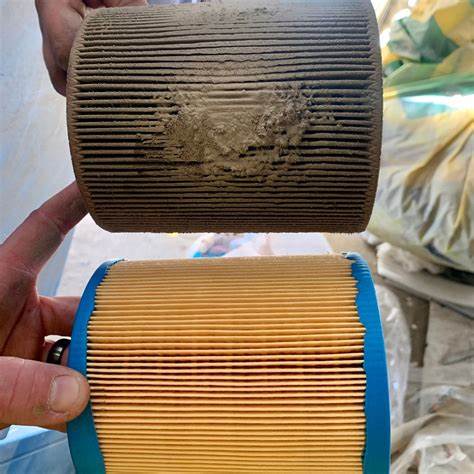
1. The Ripple Effect of Downtime: More Than Just Repair Bills
- Lost production time and missed deadlines.
- Overtime pay for rushed repairs.
- Damaged reputation and customer dissatisfaction.
- Potential for product spoilage or quality issues.
- Keywords: lost productivity, manufacturing downtime, operational costs, emergency breakdown.
2. Small Parts, Big Problems: Commonly Neglected Components
- Air Filters: Clogged filters strain the motor and reduce airflow.
- Oil Filters: Failure can lead to contaminated oil and premature air end wear.
- Oil Separator Elements: A compromised separator leads to oil carryover, air quality issues, and potential damage to downstream equipment.
- Thermostatic Valve Kits, Check Valves, Pressure Sensors: These seemingly minor parts can cause major system failures if they malfunction.
- Keywords: air filter replacement, oil filter failure, oil separator element change, thermostatic valve, check valve problems.
3. The Pitfalls of Reactive Maintenance: A Costly Cycle
- Explain how waiting for a failure always costs more than preventing it.
- Higher labor costs for emergency service.
- Increased cost of expedited parts shipping.
- Risk of secondary damage from a failed component.
- Keywords: reactive maintenance, emergency compressor repair, costly breakdowns.
4. The Unquestionable Value of OEM Parts
- Discuss why using Original Equipment Manufacturer (OEM) parts ensures compatibility, optimal performance, and maintains warranty.
- The risks of using aftermarket or generic parts (reduced lifespan, poor fit, voided warranties).
- Keywords: genuine compressor parts, aftermarket vs OEM, warranty protection.
5. Implementing a Proactive Maintenance Schedule
- Importance of following manufacturer recommendations for service intervals.
- Benefits of a comprehensive Preventative Maintenance (PM) program.
- Consideration of service contracts for peace of mind.
- Keywords: compressor service schedule, preventative maintenance program, compressor service contract, routine compressor checks.
6. Recognizing Warning Signs: Don’t Wait for Catastrophe
- Unusual noises (knocking, grinding).
- Increased power consumption.
- Fluctuating pressure or reduced airflow.
- Oil leaks or excessive oil carryover.
- Keywords: compressor troubleshooting, warning signs, abnormal noise, pressure drop.
Conclusion:
- Summarize that investing in proactive parts replacement is not an expense, but an investment in reliability and profitability.
- Empower readers to take control of their compressor’s lifespan.
- Call to action: Contact us for a PM plan, genuine replacement parts, or a maintenance consultation.